Anti Collision System
For Tower Crane Zone Protection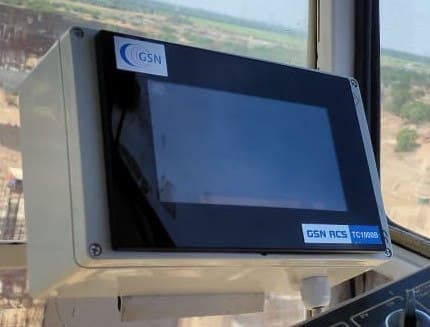
-
Tower Cranes are widely used for lifting operations in the construction industry across India. Multiple Tower Cranes are being installed in order to increase the speed of construction, this adds challenges to crane operators.
-
Many cranes are sharing common zones, which are known as collision zones. Little ignorace can lead to severe damage during operations in collision zones. As per statistics, tower cranes contribute to quite a number of serious accidents.
-
Property damage and bodily injuries can be avoided if the operators are properly informed about collision zones and possible collision detection in advance by means of audio visual alarms.
-
ACS provides neccesary details about collision zones with status & positions other cranes and obstacles in crane perifery by its display and audio alarms. This helps in safe operation of tower cranes in collision zones by alerting operator on detection of collision possibility.
-
ACS is also equiped with speed reduction and swing trip in order to avoid collision between cranes.
-
ACS is capable of being used with upto 11 Cranes with one Master Crane.
-
Long range radio modem is used for data exchange. (Freeband Frequency Operated)
-
Data logging function constantly collects and saves events related to the management of prohibited zones and interference functions.
-
Screen displays information about the crane movement, trolley position and movement of the other cranes, static obstacles and other general information required by operators.
-
ACS works on zoning, anti-collision and data logging functions. The zoning function controls the working limits of a tower crane to avoid collisions.
-
ACS is also equiped with self diagnostic features such as:
Radio Communication Failure, Slewing Sensor Open, Trolley Sensor Open, Motor Feedback Open, Zero Shift, Power Supply Failure.
Display of ACS System
-
LOREM IPSUM IS SIMPLY DUMMY TEXT OF THE PRINTING AND INDUSTRY.LOREM IPSUM IS SIMPLY DUMMY TEXT OF THE PRINTING AND INDUSTRY.
-
LOREM IPSUM IS SIMPLY DUMMY TEXT OF THE PRINTING AND INDUSTRY.